润滑油常见的三大污染物及检测方法
润滑油被誉为设备的血液,流淌在设备内部,对设备起到润滑减磨、冷却、清洁和防锈等作用。润滑油如果受到污染,会造成润滑失效,设备磨损加剧,进而引起设备故障、缩短设备使用寿命。
润滑油受到污染是一个复杂的问题,有时候日常检查可以发现,有些情况却不能,有些污染不能通过肉眼观察到。而且,对于所有的污染,等到肉眼都能发现时,说明已经很严重。总之,润滑油的污染,要早发现,早处理,尤其对于较为敏感、比较关键的设备。油液检测通过检测油品,可以准确的分析润滑油里的污染物,就像通过血液检测,发现人体的异常情况一样。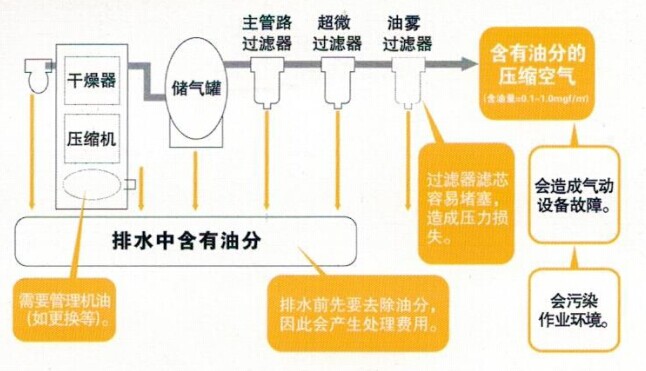
颗粒物
颗粒物是危害大的一种污染物,它们进入润滑系统内部,会造成磨粒磨损、金属压伤刮伤、金属疲劳。颗粒物一般具有一定的硬度,许多颗粒物的尺寸很微小,能穿过零件之间的间隙,在设备内部循环,造成磨损。常见的颗粒物有灰尘、砂砾、设备运转中产生的细小金属颗粒、锈渣等。
颗粒物污染不但危害设备本身,而且还会缩短润滑油的使用寿命。磨粒磨损会增加油里的金属粉末含量,这些细小的金属颗粒不但进一步磨损设备,而且还会加速润滑油氧化变质,因为金属粉末会催化油品的氧化速度。鉴于这些颗粒物的危害是连锁性的,因此及早监测、及早处理很重要。
油液检测可以发现油液里的细小颗粒物,还可以发现设备的早期磨损。通过检测油液里的颗粒物计数,可以了解油液的清洁度、是否进入了颗粒污染物。另外,通过金属分析,可以发现设备的早期磨损。当颗粒物与设备的金属发生了磨粒磨损,被刮擦下来的金属就可以被监测到。通过金属的成分分析,还可以找到磨损源。例如,齿轮的材料大部分是铁,还有少量的其它合金成分(铬、镍、锰等)。
如果发现颗粒物进入润滑油,一般的补救措施包括:找到颗粒物从哪里进来的,然后堵住来源;通过过滤,把颗粒物除掉。但是,这个做法不一定都有效。有些时候滤油也很难完全除掉颗粒物,还得把油换掉。如果磨损比较明显,建议进行铁谱分析,可以确定磨损的程度,指导设备维护。
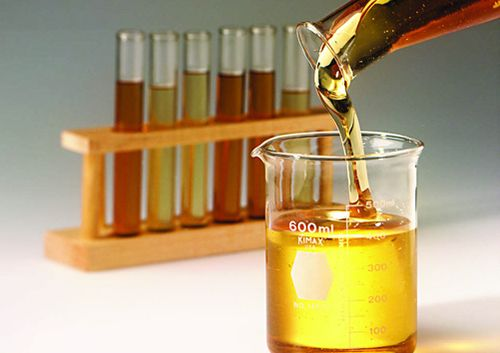
水分
水分是常见的污染物,虽然危害没有颗粒物严重,但是水分会破坏润滑效果,使油变质,造成设备磨损,水分也会引起金属锈蚀。润滑油里的水分有三种形式:溶解水、乳化水、游离水,其中,乳化水的危害大。
溶解水就是已经溶解在润滑油里的水分,润滑油具有吸湿性,会吸收空气里的水分,因此会含有少量的水分。一般来说,少量的溶解水不会造成什么危害,除非某些情况对润滑油的含水量要求特别严格。润滑油可以允许的溶解水含量大值为吸水饱和点,在达到吸水饱和点之前,润滑油里虽然含有水分,但是不会表现出有水的迹象,例如乳化或者浑浊、透明度降低等。
润滑油里进入水后,如果没有和油分离开,微小的水滴悬浮在油液里成为悬浊液,就成为乳化水,乳化水的危害大。当润滑油乳化时,含水量已经超过了饱和点。油里含有乳化水时,润滑油的透明度会降低、浑浊,颜色发白甚至变成奶白色。乳化水的危害很大,因为它们可以自由地流动,污染整个润滑系统里的油,另外,水分会破坏油的润滑性。乳化水到达设备运转的承压区域后,这些区域会因润滑不良摩擦加剧而磨损。
当水和润滑油完全分离开后,就成为游离水。游离水的危害相对较小,但是也会引起问题。首先,游离水也可能随着润滑油循环,引起油乳化。另外,油里的水会削弱润滑油的破乳化性,导致泡沫增加,消耗润滑油里的添加剂,缩短润滑油的使用寿命,并且容易滋生细菌。
水分对设备的危害除了引起润滑不良,还有氢脆、锈蚀。润滑油能防止金属锈蚀,如果油里进水,容易引起金属锈蚀。
氢脆又称为氢损伤,可以引起轴承损坏。水会分解为氢和氧,电解和腐蚀也会产生氢,水会促进电解和腐蚀,高强度钢尤其容易遭受这种问题。另外,润滑油、润滑脂里加入的添加剂里面含有硫(添加剂、抗磨剂等等),矿物油本身也含有一定的硫杂质,会促进金属的腐蚀和裂化。潮湿的大气和游离的水分都可能引起金属的氢脆问题。
水分会破坏油膜的强度和油膜的完整性,润滑是依靠油在金属接触面之间形成一层油膜,油膜隔开金属之间的直接摩擦,防止金属直接接触。如果水分进入轴承的金属接触受力区域,就会破坏油膜的完整性,降低油膜强度,导致润滑不良或者金属之间直接摩擦,会引起金属疲劳损伤,形成金属刮擦、碎裂。
水会缩短润滑油的使用寿命,另外水还会造成润滑油里的抗氧化剂流失、消耗,导致润滑油氧化变质。润滑油氧化会形成酸性物质、油泥和漆膜,使油的黏度增加,影响喷溅润滑的效果等。
在现场,可以观察润滑油的外观,如果润滑油透明度降低、发白、浑浊或者乳化,就说明油里进水。另外,加热法也是简单易行的方法。这个方法可以进行基本的判断,操作简单。使用一块铁片,在火上加热到130℃左右,在铁片上滴入一滴润滑油,如果有水分会观察到气泡,因为油里的水分受热蒸发引起的气泡。气泡越大、数量越多,说明含水量越多。如果看见气泡还能听见劈啪的爆裂声,说明含水量相对较多,可能已经达到了2000ppm以上。不过,加热法只适用于测定乳化水和游离水。
卡尔费休水分检测是精准的水分检测方式,游离水、乳化水、溶解水均可检测,操作得当的情况下,对水分的检测可以量化到0ppm(0.001%)的级别,一般的工业监测和精准的工业监测都可以使用。
当发现润滑油进水时,正确的处理方法是首先找到水分来源,切断来源,然后采取除水措施,严重时需要换油,通过油液检测来确定。
混入其他油
使用润滑油时,应该避免与其它油品接触。但是有些情况,比如泄露、加油时用错润滑油(润滑油粘度选择错误或者添加剂类型选错)等等,都会造成不同的润滑油混合。
例如,矿物油与常规的PAG合成油(非油溶性PAG)不能相容。这两种油如果相混,会导致混合后的油粘度增加,并形成油泥,其它现象还有酸值升高、滤芯被油泥堵塞。同时,由于发生相混致润滑不良,还会发生设备磨损。
当润滑油里混入其他油类,解决的方法是换油并冲洗润滑系统,不能使用过滤的方法除掉。
使用错误配方类型的润滑油也是一个常见问题,可能是换油时不小心加错油,或者直接就是选油错误。例如,如果设备需要的是润滑油(EP)或者抗磨型润滑油(AW),而用户误加成一般的抗氧防锈型油品,就会造成设备运行中磨损。
如果对润滑油的抗乳化性有较高要求的设备里,混入了加有清净分散剂的油品,那么油的抗乳化性/油水分离性会削弱。例如汽轮机油里混入了发动机油,1升的机油混入7000升的汽轮机油里,就可以破坏汽轮机油的抗乳化性,因此千万要避免润滑油相混。对于这种情况,需要把油都换掉,并且冲洗润滑系统。
又如,如果设备有黄色金属(例如铜),需要使用润滑油,那么就需了解润滑油对黄色金属的腐蚀性,因为某些润滑油里含有活性硫,会腐蚀黄色金属。
通过红外图谱检测,可以发现润滑油误用或者相混。另外,还配合使用铁谱分析,可以发现是否发生了设备磨损。因为润滑油误用或者混合,很可能带来设备磨损。
润滑油误用还可能是粘度不对,有可能是粘度选择错误,或者油里混入了其它粘度的油。如果油的粘度过大,或者混入了高粘度油,在齿轮系统里会观察到磨损,还有喷溅润滑异常。 对于液压系统,会造成设备反应迟缓,油的滤过率降低。
对于油的粘度低的情况,几乎都会发生设备磨损。
如果怀疑润滑油的粘度不对,可以进行粘度检测。另外,还可以再进行金属元素检测,因为粘度不同的润滑油,哪怕是同一个产品系列,添加剂的含量也会有差别(添加剂里含有一些金属元素)。
如果润滑油的粘度不对,建议的处理方法是把油换掉。对于油量很大的系统,则需部分置换新油,逐步换上适合粘度的润滑油。
采用微油空压机,产生排油排水处理费用
从微油压缩机中排出来的水中含有油分,因此需进行妥善的排水处理,产生排水处理的费用,即环保又经济。
【条件】
空气温度:30℃、相对湿度:70%
产气量:1600L/min、压力:0.8Mpa(举例)
干燥加压露点:12℃
负载比例:80%
运行时间:15小时/日、300日/年
排水处理费:2.3元/日
壹年费用1.6万元